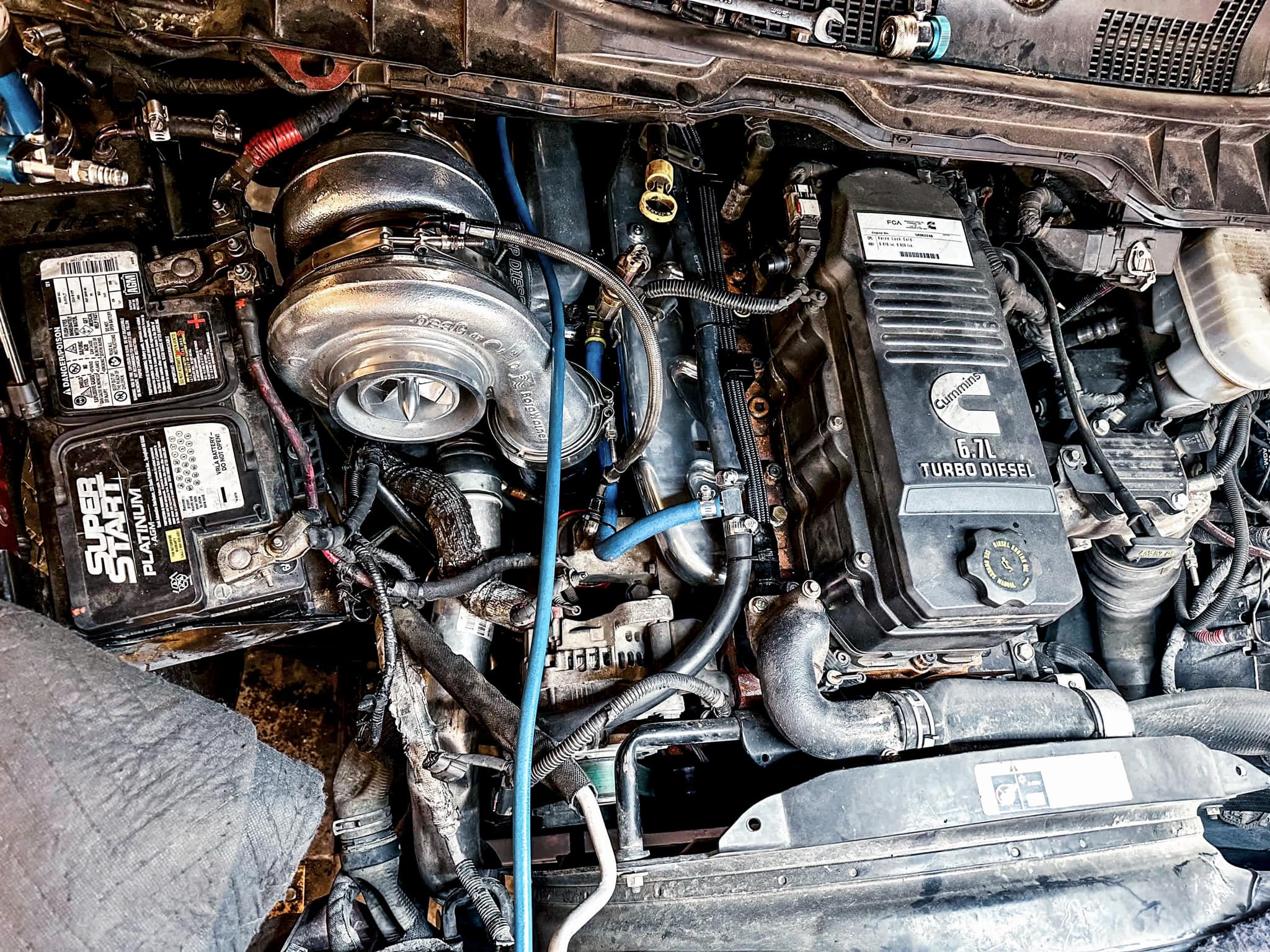
Why Fleets Need a Dedicated Dry Bulk Repair Shop
Discover why a dedicated dry bulk repair shop is essential for fleet efficiency, safety, and DOT compliance. Reduce downtime with specialized pneumatic and hydraulic repairs.
When it comes to dry bulk transport, fleets are dealing with highly specialized equipment that requires precise maintenance and repairs. Unlike general freight, dry bulk involves pneumatic tankers, auger trailers, and hopper bottoms, all of which have complex air and mechanical systems. A dedicated dry bulk repair shop ensures that these unique components receive expert attention, minimizing downtime and keeping operations running smoothly.
The Role of Pneumatic Systems in Dry Bulk Transport
Most dry bulk tankers use pneumatic (air-powered) unloading systems, which rely on blowers, compressors, and aerators to efficiently move materials. These systems must maintain precise pressure levels to prevent clogs, product contamination, or a complete unloading failure. A general diesel repair shop might understand basic air systems, but a dedicated dry bulk repair shop is equipped to troubleshoot these components quickly, preventing prolonged downtime.
- Blower Maintenance: Pneumatic tankers use blower systems to create the necessary air pressure to move dry goods through the piping system. These blowers experience extreme heat and friction, requiring regular lubrication, belt inspections, and pressure testing.
- Aeration Systems: Inside the tanks, aeration pads ensure product flows smoothly. If these become clogged or worn, unloading becomes slow and inefficient, leading to delays and potential load rejections.
- Air Compressor Failures: The air compressor powers the entire unloading process. A failing compressor results in pressure loss, meaning the trailer can’t discharge its load efficiently. Regular maintenance ensures optimal pressure levels are maintained at all times.
2. Structural Integrity: Tank Inspections & Repair
Dry bulk trailers don’t just rely on mechanical and pneumatic components—they also have strict structural requirements. Because these tanks handle high-pressure unloading and delicate materials, even minor damage can lead to serious safety and operational issues. Routine inspections and repairs by a specialized repair team ensure that the structural integrity of each trailer is up to industry standards.
- Weld Cracks & Corrosion: The constant pressurization and exposure to different materials can cause cracks in welds or corrosion in the tank body. A dedicated shop inspects and repairs these issues before they lead to catastrophic failures.
- Seal & Valve Failures: The hatches, gaskets, and discharge valves must be airtight to prevent product contamination. If a seal fails, moisture or foreign materials can enter the tank, leading to load contamination.
3. Hydraulic System Repairs for Auger & Hopper Trailers
Not all dry bulk trailers rely on pneumatic unloading. Auger and hopper trailers use hydraulic systems to move bulk materials. These hydraulic systems need consistent pressure levels, clean fluid, and well-maintained lines to prevent leaks and mechanical failure. A general repair shop may overlook these components, but a dedicated dry bulk repair shop ensures your hydraulic systems are always operating at peak efficiency.
- Hydraulic Cylinder Leaks: Even a small leak in a hydraulic system can lead to pressure loss and system failure.
- Hose & Fitting Wear: Over time, hydraulic hoses and fittings wear out, causing fluid contamination and decreased performance.
- Pump Efficiency: The hydraulic pump needs to be tested regularly to ensure it’s pushing adequate fluid pressure for unloading operations.
Minimizing Downtime with Proactive Maintenance
For any fleet, time is money. If a dry bulk trailer is sitting in a shop waiting for repairs, it’s not making deliveries. A dedicated dry bulk repair shop understands the urgency of repairs and offers preventative maintenance plans to avoid major breakdowns.
1. Preventative Maintenance Plans
With regular inspections and proactive maintenance, fleets can avoid emergency breakdowns and keep their trailers running efficiently. By partnering with a dedicated repair shop, fleet managers can implement scheduled maintenance programs that address:
- Blower lubrication and belt replacement
- Valve and gasket inspections
- Tank pressure testing
- Structural weld and integrity inspections
- Hydraulic system checks
2. On-Site Repairs & Mobile Service
A specialized dry bulk repair shop often offers on-site and mobile repair services, reducing the need to bring trailers into the shop for every small issue. This is especially useful for large fleets operating in multiple locations, as technicians can perform minor repairs and diagnostics on-site, keeping downtime to a minimum.
Regulatory Compliance & Safety Considerations
The Department of Transportation and other regulatory bodies require dry bulk trailers to meet strict safety and environmental standards. Failure to comply with these regulations can lead to fines, failed inspections, and even vehicle out-of-service violations. Working with a dry bulk repair specialist keeps fleets safe and compliant. A specialized repair shop ensures that fleets remain compliant with federal and state regulations, including:
- Tank pressure certifications
- DOT-mandated inspections
- Blower and air system leak detection
- Hopper and valve contamination prevention
The Competitive Advantage of a Dedicated Dry Bulk Repair Shop
When fleets invest in specialized repair services, they see long-term benefits in operational efficiency, cost savings, and fleet reliability.
- Faster Turnaround Times: A dedicated dry bulk repair shop has the necessary parts, tools, and expertise to diagnose and fix issues faster than a general repair shop. This means less downtime and more time on the road.
- Extended Equipment Lifespan: Proper maintenance extends the life of expensive blowers, compressors, hydraulic systems, and tanks. Fleets that regularly service their equipment save money in the long run by preventing major mechanical failures.
- Reduced Repair Costs: By catching problems before they escalate, fleets spend less on emergency repairs and avoid expensive part replacements.
- Improved Driver Satisfaction: Well-maintained trailers mean fewer breakdowns, better efficiency, and improved safety—all of which contribute to driver satisfaction and retention.
A Dedicated Dry Bulk Repair Shop
The complexity of dry bulk transport demands specialized care. Relying on a general diesel repair shop can lead to inefficient maintenance, higher repair costs, and unexpected downtime. A dedicated dry bulk repair shop ensures that pneumatic systems, hydraulic components, and tank structures receive expert attention—keeping your fleet running smoothly.
Don’t leave your maintenance to chance with Southeast Fleet Services. If you operate a dry bulk fleet in North Carolina, South Carolina, or Georgia, invest in specialized repairs to maximize uptime, safety, and profitability! For more information about the industry, read our article on ways to improve dump truck efficiency.
Locations & Contact Info
Welcome to Southeast Fleet Services, your premier heavy-duty diesel repair shop in North Carolina, South Carolina, and Georgia. Give us a call today at one of our five locations to set up specialized services and repairs for your heavy-duty vehicles and equipment.